Plywood is a revolution in the construction world. It is always discussed whether plywood is strong or wood? In this post, we will know why plywood is strong.
Plywood was introduced into the United States in 1865. But there was no standard size. In 1928, a standard size was fixed at 4 ft by 8 ft (1.2 m by 2.4 m), which was started by the plywood companies. When plywood was introduced in the United States, it was used as a building material, but today it is widely used in almost all constrictions.
What is Plywood?
Plywood is an engineered construction material made from multiple thin sheets of wood veneer glued together to form a strong and stable panel. It is commonly used in construction, furniture making, and other woodworking projects.
Why is Plywood So Strong?
Plywood gets its strength from the composition of the veneer and the way it is made. So here are some factors that make plywood more sustainable than many other construction materials.
Flexibility
If we apply the same pressure on the surface of wood and plywood of the same thickness, the wood may crack and break, while the plywood only bends and return to the same position.
Plywood is more flexible than wood to distribute the pressure evenly over the entire surface and remain stable.
Multiple Layers
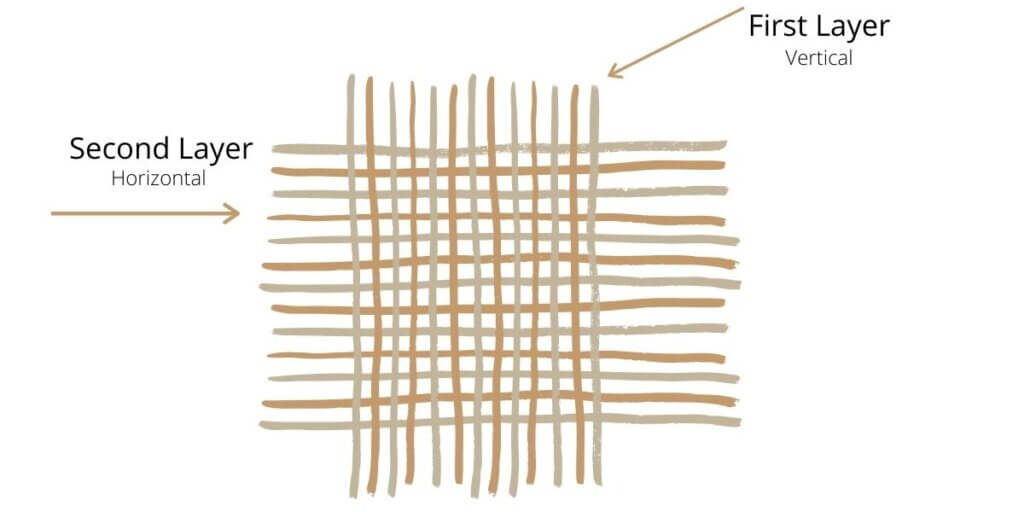
Plywood is made with multiple layers, or plies, of wood veneer. All these layers are placed crosswise to each and glued with powerful adhesive.
Crossing adjacent sheets distribute equal strength in all directions, making it much stronger than wood.
Regular Quality Improvements
Plywood is an engineered material that is constantly being improved. It was not always strong and durable. Plywood manufacturing companies spend thousands of dollars each year to enhance plywood quality.
Fewer Knots and Defects
Because plywood is made from thin sheets of wood veneer, defects and knots that weaken solid wood can be cut out or avoided in the manufacturing process.
How is Plywood Made?
There are several step-by-step processes for making plywood. In this blog section, I will share the following steps.
- Well-dried logs are debarked and then peeled into thin sheets of veneer using a rotary lathe or a knife. There is no strength in these thin layers of wood. They are so weak that they can be torn with light hands.
- The veneers are graded and sorted according to quality, thickness, and grain pattern. Sheets with extra knots or defects are removed.
- Veneer sheets are cut to size and glued together with the grain of each layer running perpendicular to each other. This cross-graining technique helps to make the plywood stronger and more stable.
- The glued sheets are pressed under high heat and pressure to ensure a strong bond between the layers of the plywood.
- Plywood sheets are sanded to make a smooth surface, and edges are trimmed.
- Plywood is treated for many hours in a large boiler to make the plywood rot and moisture-resistant.
- Finally, it is ready for packaging and shipping.
Read other articles
Comments are closed.