Plywood is an important material for the furniture and construction industry. There are many types of plywood that are used in different places. But marine plywood is the highest grade of plywood used for long-term use.
Marine plywood performs quite well in both dry and wet places. Also, the chances of termites and fungus inside it are very less. It is durable for a long time under any weather condition. Durable face and core veneers are used to make marine plywood.
Many people think that marine plywood is waterproof plywood. But this is not true, marine plywood is not 100% waterproof. The quality of marine plywood is better than that of normal plywood. Due to its quality, this plywood is used in making boats and boat parts.
The Advantages of marine plywood
1. Good Water Resistant
Marine plywood is good and water-resistant. It is also long-lasting after exposure to water. Therefore it is useful for making parts of boats and ships. But it is not completely waterproof, so it needs to be changed after a few years or a couple of decades.
If you are using Marine Plywood for an indoor and outdoor project, then it can run for decades.
2. Surface finish
Marine plywood is made from solid veneer wood. Because of this, the surface of the plywood is quite fine and gives a wooden appearance.
Plywood can also be used without any paint and mica. But using paint and mica makes it more durable.
Being a smooth surface, it holds the laminate well. Being a fine surface, paint and polish can be easily done after grinding sandpaper with light hands.
3. Durability
Marine plywood is more durable than normal plywood; it maintains its strength even in bad weather. It has remained sustainable for several decades in exterior and interior projects.
4. Flexibility
This plywood is made of many thin pieces of wood. Because of this, it can be easily folded as per requirement. Marine Plywood is strong as well as flexible. So that when it is pressed more on the plywood, it turns and does not crack like wood.
5. Uniform Strength
The plywood does not have knots, so there is general strength throughout the plywood. Douglas fir wood is used to make marine plywood, which has knots but does not have holes in knots, so it is strong. While manufacturing plywood, Each of the other veneer layers is placed in the cross of the first. This method makes it stronger.
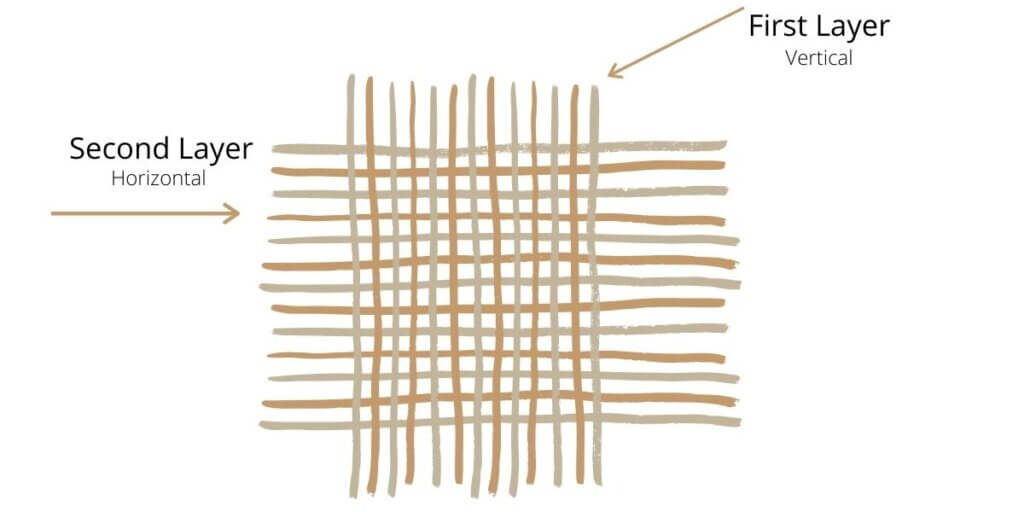
6. Availability
Marine Plywood is easily available in the wood market. It is available in many thicknesses and lengths. This is available in large sizes compared to solid wood. It is available in various thicknesses ranging from 6 mm to 32 mm.
There is no joint of any kind in its sheet. Due to it being a solid sheet, its maintenance is much easier.
7. Good Density
Marine Plywood having a good density and holds the screw and nail very well.
8. Good Termites Resistant
Chemicals are used to protect marine plywood from termites and ants. Because of this, there is no need to care much about marine plywood.
The Disadvantage of Marine Plywood
1. Price
It is more expensive than Medium Density Fiberboard (MDF) because there are many processes in its manufacturing. Like extremely high heat and pressure treatment.
2. Bend issue
As we know, it is made of thin layers. Therefore, it bends when it is overloaded. Support is required to prevent this. When we use a large sheet without any support, it is prone to bend.
3. Not Waterproof
Marine plywood is not 100% waterproof, although it is made from hardwood, which makes it perform well when exposed to water. But can’t stand humidity or extreme weather for a long time.
4. Hard to Identify
It is difficult for a common person (who needs to learn more about wood and furniture) to determine whether good or bad wood veneer has been used to make plywood.
5. Chemicals
Marine plywood is chemically treated to protect the wood veneer from termites and ants and make it more durable, but these chemicals harm humans and animals.
To avoid its harmful effects, while cutting the plywood, you must wear gloves on your hands and apply eyeglasses. It is very harmful to asthma patients.
6. The edges also need to be covered with wood
Plywood has very sharp edges, small particles of wood start coming out from this edge. These particles can scratch. Therefore, a thin wood strips is applied to the edges of the plywood to cover the edges.
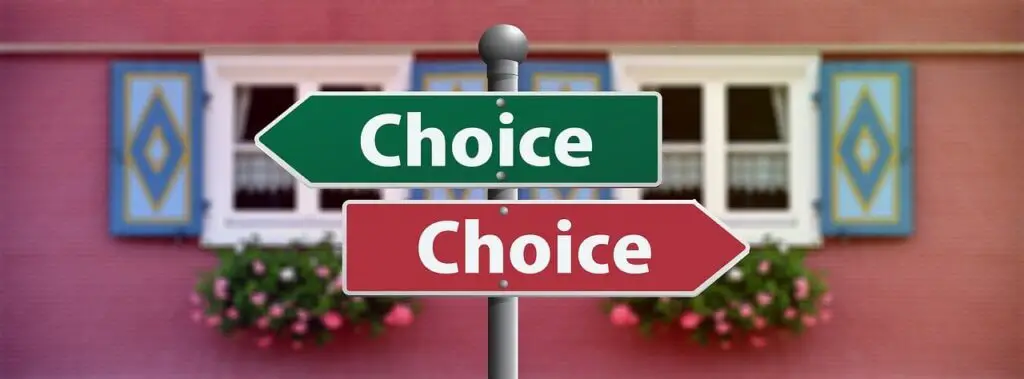
So these were the advantages and disadvantages of Marine Plywood, you can choose another alternative material in place of Marine Plywood which is available in the market. Now let’s see some options.
Alternative to marine grade plywood
Ribbon Grain Plywood, Fiberboard, Fiber Cement Board can be the best Alternative for Marine Plywood.
1. Fiberboard

Fiberboard is a well-known material we can use in place of marine plywood. The fiber of wood is mixed with wax to make a fiberboard material. After drying, it becomes a solid plywood-like material and is treated with extremely high heat and pressure to make it more durable.
2. Ribbon Grain Plywood
Ribbon Grain Plywood is named because of its grain. It is a sheet of wood with a smooth surface. Because of this, there is no need to spend much on its paint and polish to improve the texture. The installation process is also easy.
It is less strong than marine plywood, but it is a good alternative to Marine Plywood.
3. Fiber Cement Board
The Fiber Cement Board is made by mixing cement and wood fibers. The Hatschek process is used to make this board. It is mainly used in Internal / External Walls, Internal Wall linings, False Ceilings, Eaves & Soffit Lining, Facia, and Duct Coverings, Prefabricated Shelters, Roof Tile Underlay, and Flooring Substrate.
Here we saw the Marine Plywood Advantages And Disadvantages. I hope it helps you if you have any suggestions, comment in the comment box.
FAQ
How Marine Plywood is made and Why it is Stronger?
Marine plywood is made in the same way as standard plywood, but in the manufacturing of marine plywood, additional measures are taken to make it more water-resistant and durable than traditional plywood.
- Selection of high-quality hardwood veneers.
- Use waterproof glue, such as phenolic formaldehyde or epoxy.
- Hot pressing the layers of veneers together to create a strong and stable panel.
- Treating the surface and edges of the panel with waterproof coatings or sealants to make water-resistant.
Marine plywood is strong because it is made with high-quality veneers and glue. Read Why Is Plywood So Strong Compared To Others?
Comments are closed.