Laminated veneer lumber (LVL) is an engineered wood construction product. LVL is made of multiple veneer sheets and assembled with waterproof adhesives. It is used in headers, beams, rim boards, truck bed decking, roadway signposts, trusses, and many other applications.
LVL is an innovation for the construction sector. This is such an engineering discovery that is proving to be a boon in the world of construction. It is spreading rapidly across the globe.
Production of LVL began in 1941. It was first made from 3.6 mm thick Sitka spruce veneer. Due to the great demand for LVL, the USDA Forest Products Laboratory conducted research and development to improve its efficiency.
Experts say that Douglas fir wood is a perfect wood for LVL, but different woods are used in different countries. Yellow poplar and other softwoods are used in the United States. Wood is chosen according to their application. LVL has the highest production in America.
Laminated Veneer Lumber Uses
Beams and Rafters
Laminated veneer lumber is widely used to make beams and rafters. Beams and rafters are often exposed to weather and storms. In such a situation, it is important to be durable and bear heavy weight.
LVL Wood Flooring
Laminated veneer lumber is more commonly used in framing wood floors. Laminated veneer lumber (LVL) is compatible with I-joist floor framing. I-joists are used extensively in floor and ceiling framing. I-joists are strong and lightweight, saving builders the hassle of maintaining and levelling floors.
The I-joist frame has two parts: the web and the flange. The web is the part between the upper flange and the lower flange. The web and flange together form the shape of a capital (I). That’s why they are called I-joists. I-joists need to be installed carefully. Otherwise, structural failure may occur.
Rim Boards and Edge Forming
LVL can be used as rim boards to provide lateral support to the edges of floors, roofs, and walls. It is also suitable for creating straight and stable edges in construction applications.
Components for the Door and Window
As we know, LVL is twice as strong as the ordinary lumbar. LVL is widely used for exterior doors and windows.
Laminated Veneer Lumber Advantages
High Surface Quality
The laminated veneer lumber gives high surface quality. The defective wood and knots are cut and removed while peeling veneer from the wood logs during veneer assembly or gluing. The production company keeps the heartwood and good texture veneer at the top.
Good Thermal Performance
Laminated Veneer Lumber (LVL) boasts excellent thermal performance, making it particularly advantageous in colder climates. The tightly bonded wood in its construction ensures effective insulation, contributing to the retention of warmth in both roofs and floors crafted from LVL.
Stability and Durability
Laminated veneer lumber (LVL) is a durable and stable option for long-term flooring and roofing. It is more rot-resistant than regular wood and can withstand long periods of moisture, water, and air, ensuring long-term stability.
Versatility
LVL is a versatile material; its uniformity and strength make it suitable for a wide range of applications, from beams and headers to joists and rafters, providing flexibility in design and construction.
Laminated Veneer Lumber Disadvantages
Price
Generally, laminated veneer lumber costs more than ordinary lumber. The advanced manufacturing processes and materials used contribute to an increased upfront expense.
Weight
Laminated veneer lumber weighs more than traditional lumber because it has no hollow parts. It is made of solid veneer. Working at height can be difficult due to weight.
Hard to Work
Laminated veneer lumber is challenging to work with because it is denser and heavier than traditional lumber. Therefore, it is difficult to cut, nail, and screw.
Limited Availability of Large Sizes
In certain regions, finding LVL in large sizes might be challenging. This limitation can constrain certain construction projects requiring extensive or oversized structural components.
How is Laminated Veneer Lumber Made?
1. Harvesting and Debarking
In the first stage, mature trees are harvested from the forest. After that, the debarking process is started with wood logs. Debarking is the process of removing bark from wood.
Large stationary or portable machines are used in this process. The entire log of wood is passed through a sharp and serrated blade, which removes the bark while turning the wood logs.
2. Steaming
Steaming is a process to improve the appearance of the sapwood and heartwood as well as increase the rot and moisture resistance of the wood.
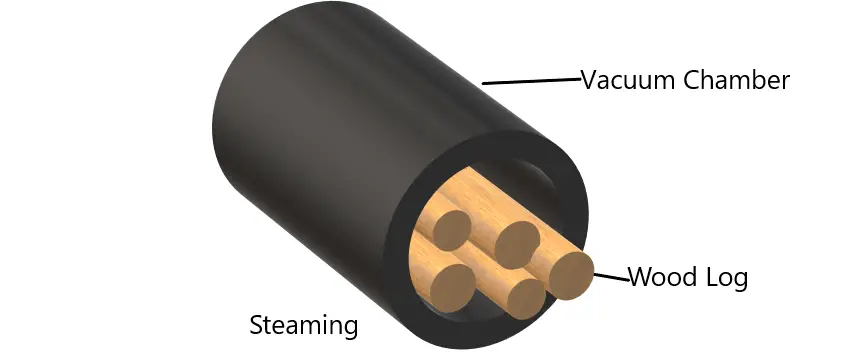
When the wood cell of a tree is formed, it is white in color and wide open. Because of the wide-open cells, fluids can easily reach the leaves from the roots. So this helps in growing trees. It is on the outside of the tree, and heartwood is on the interior of the tree. Many people do not like it because of the white color and the weakness of the sapwood.
In this process, wooden logs are treated with chemicals in a large cylinder/vessel. High heat and pressure are used along with chemical steam. This process usually lasts 48 hours or more. Different production companies use their steaming techniques.
3. Peeling Veneer
In this stage of LVL production, larger log pieces are peeled and converted into thin veneer sheets using rotary peeling technology. The thickness of the veneer sheet can be from 2.5mm to 4.8mm.
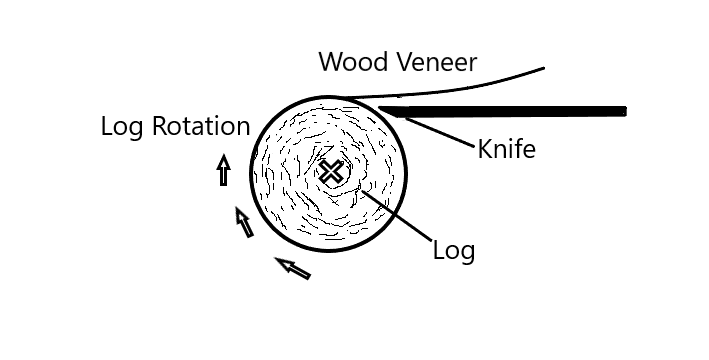
In this process, the wooden log is rotated at right angles with a sharp blade. The angle of the blade depends on the thickness of the veneer sheet.
4. Drying, Trimming, and Grinding
It is very important to dry the veneer sheets before moving on to the next process. Hot air is fired over the veneer through several nozzle sprays. After this process, the thickness of the veneer reduces, but it is much less.
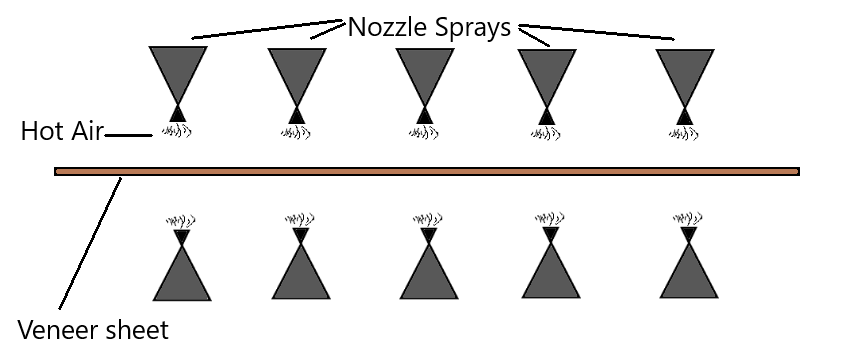
Next is trimming process, the veneer sheet is trimmed around the sides to smooth the edge and give the veneer the correct shape.
In the next step, the grinding of lumber is done with the help of sandpaper. In this process, the surface of the wood is made smooth so that the final work can get a smooth surface finish.
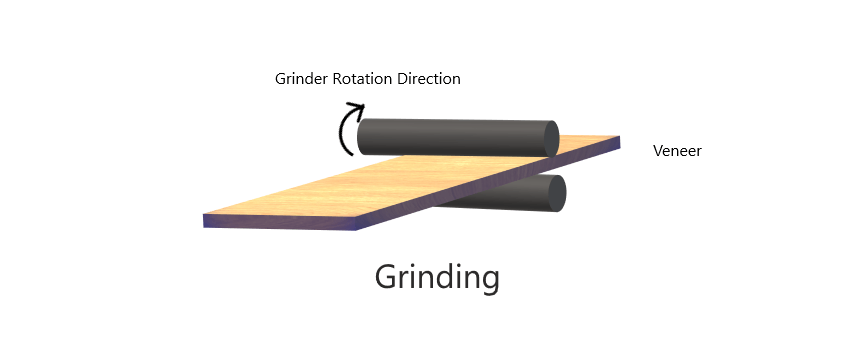
5. Adhesive Veneer Sheets
In this process, several thin veneer sheets are glued together with a waterproof adhesive. The thickness of the veneer sheet depends on the number of sheets. All the veneer sheets are placed perpendicular to each other.
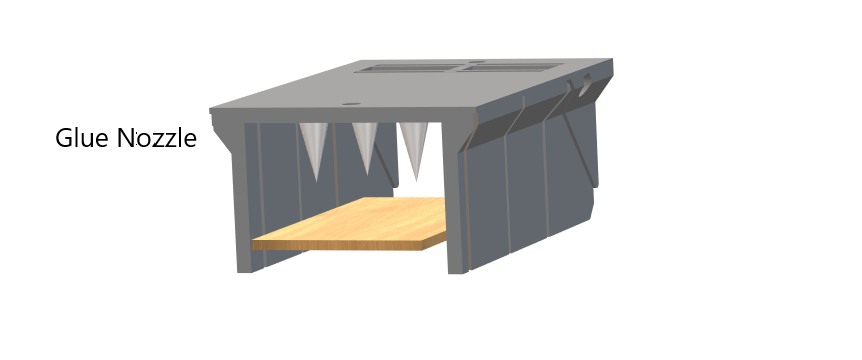
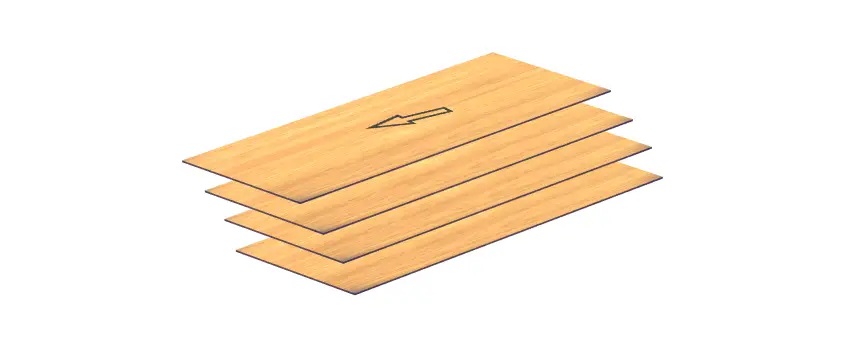
A large machine is used for this process, and it has multiple nozzle sprays. This nozzle spray continuously sprays the adhesive, and the veneer sheet slides under the nozzle spray through the moving belt. So that the glue adheres well to the veneer sheet; if the glue veneer is missed, it will be responsible for air pockets.
After the adhesive process, high heat and pressure are applied so that all the layers adhere well to each other and form a strong structure. That lasts a long time.
6. Sanding, Cutting, and Packing
The laminated veneer lumber is sanded once again. In this process, low-grain sanding paper is used so that the lumber becomes smooth and shiny.
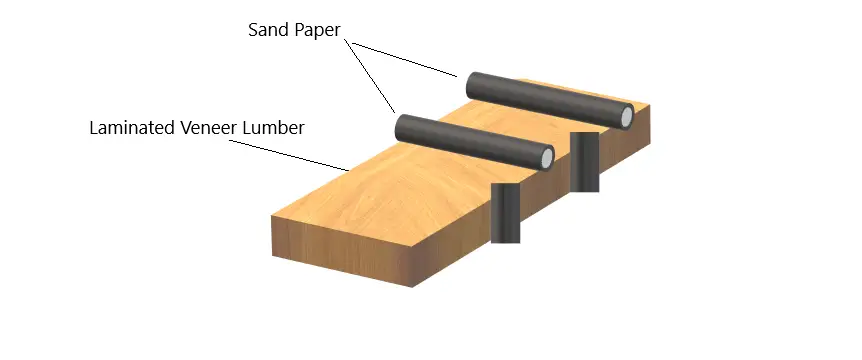
After its Sanding process, the larger structure is cut into different pieces according to the demand and application purpose.
Packing is the last step. These finished pieces are transferred to different countries as per the demand. The long-distance affects the price.
LVL vs Plywood
Plywood and LVL are very similar to each other, but dimensionally, both are completely different from each other, such as the application of each veneer and grain orientation.
Plywood
To make plywood, an odd number of veneers (3, 5, 7, or 9) are always used, and all the veneers are placed perpendicular to each other. This structure makes the plywood dimensionally more stable but does not improve mechanical properties. What I mean is that plywood cannot support a lot of load, whereas laminated veneer lumber can.
LVL
The number of veneers in LVL is more than that of plywood, and all the veneers are glued in the longitudinal direction. Due to the structure of LVL veneer, the mechanical properties are very good. LVL has similar properties to solid wood.
Strength: LVL vs Lumber
Most customers ask: Is LVL stronger than wood? The answer is…
Yes, LVL is stronger and more stable than ordinary lumber of the same species. The expert believes that LVL is two times stronger than standard framing lumber of the same dimension.
LVL can withstand 100 mph high-speed wind, so it is suitable for bad weather. At the same time, ordinary wood of the same species cannot withstand such strong wind.
The main reason for the strength of LVL is the structure of its veneers, which are laid in the longitudinal direction of each other, which makes them strong and capable of bearing heavy loads.
Are LVL Beams Waterproof?
LVL beams have excellent water resistance but are not entirely waterproof. LVL beams are made from multiple veneers, bonded at high pressure and heat with waterproof adhesives. Adhesives strengthen the beams and provide excellent water resistance but do not make them waterproof.
Nothing made of wood is 100 percent waterproof. Researchers have found a ‘Type A’ phenolic adhesive that provides a largely waterproof bond.
Long exposure will require preservative treatment and finishing with a protective coating of LVL. Generally, the wood species used to make LVL are better suited for indoor use. But LVL wood made using certain chemical treatments is perfectly suitable for outdoor use.
Conclusion
In this blog, we have shared information about LVL, including how it is made and its applications. The conclusion of this post is that LVL is an important engineering product, the discovery of which has significantly eased the world of construction.
Read another article
What is Sapele Wood? Sapele Uses, Advantages and disadvantage